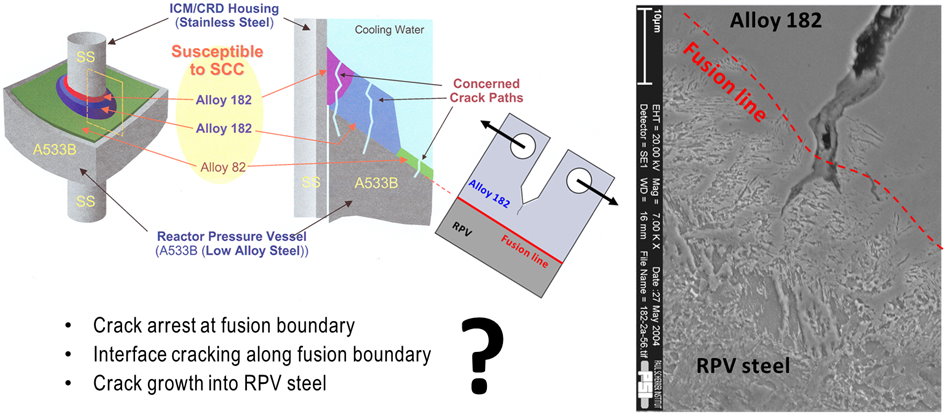
Fig. 1: Potential concern for SCC crack growth from susceptible Alloy 182 weld metal to adjacent RPV steel during BWR service. (© NACE International)
The reactor pressure vessel (RPV) is the most critical component of light water reactors with regard to plant safety and lifetime. The Nickel-base Alloy 182 is widely used as a weld filler and attachment pad metal to join the low-alloy steel RPV and RPV nozzles to both wrought nickel-base alloys and austenitic stainless steel components (piping, reactor internals) in light water reactors by manual shielded metal arc welding. The recent stress corrosion cracking (SCC) in Alloy 182 in RPV nozzles, reactor internal attachment or penetrations dissimilar metal welds in boiling water reactors (BWRs) represent a serious potential safety concern (Figure 1). [1]
The Alloy 182 weld metal is very prone to SCC and cracks tend to grow towards the RPV due to weld microstructure and residual stress profiles in these welds. Such SCC cracks thus might grow into the adjacent RPV, although the SCC was confined to the weld metal and none of the SCC cracks significantly penetrated the adjacent RPV base material in field cracking incidents so far. This is consistent with the very high SCC resistance of the RPV steel. Even after post-weld heat treatment, these highly constrained welds reveal high residual stresses resulting in a high mechanical driving force for SCC cracks that are reaching the fusion boundary region between the weld metal and RPV steel. There is thus a concern that such cracks could grow into the RPV in oxidizing BWR normal water chemistry (NWC) environment, in particular in high-sulphur RPV steels (older plants) or in case of chloride contamination of the coolant or weld repairs [1-3]. It is thus crucial to know, under which conditions these cracks could grow into the RPV. Furthermore, validated SCC crack growth disposition curves for the RPV steels are needed for flaw tolerance and integrity assessments and verification of inspection intervals of periodic in-service inspection and to demonstrate sufficient safety margins. [1]
![Fig. 2: Critical combinations of stress intensity factor KI at the fusion boundary and chloride concentration of the coolant (dashed region) for SCC crack growth into the RPV steel under BWR/NWC conditions [1]. (© Elsevier)](https://blog.secnrs.ru/wp-content/uploads/2020/10/Article3_pic2.jpg)
Fig. 2: Critical combinations of stress intensity factor KI at the fusion boundary and chloride concentration of the coolant (dashed region) for SCC crack growth into the RPV steel under BWR/NWC conditions [1]. (© Elsevier)
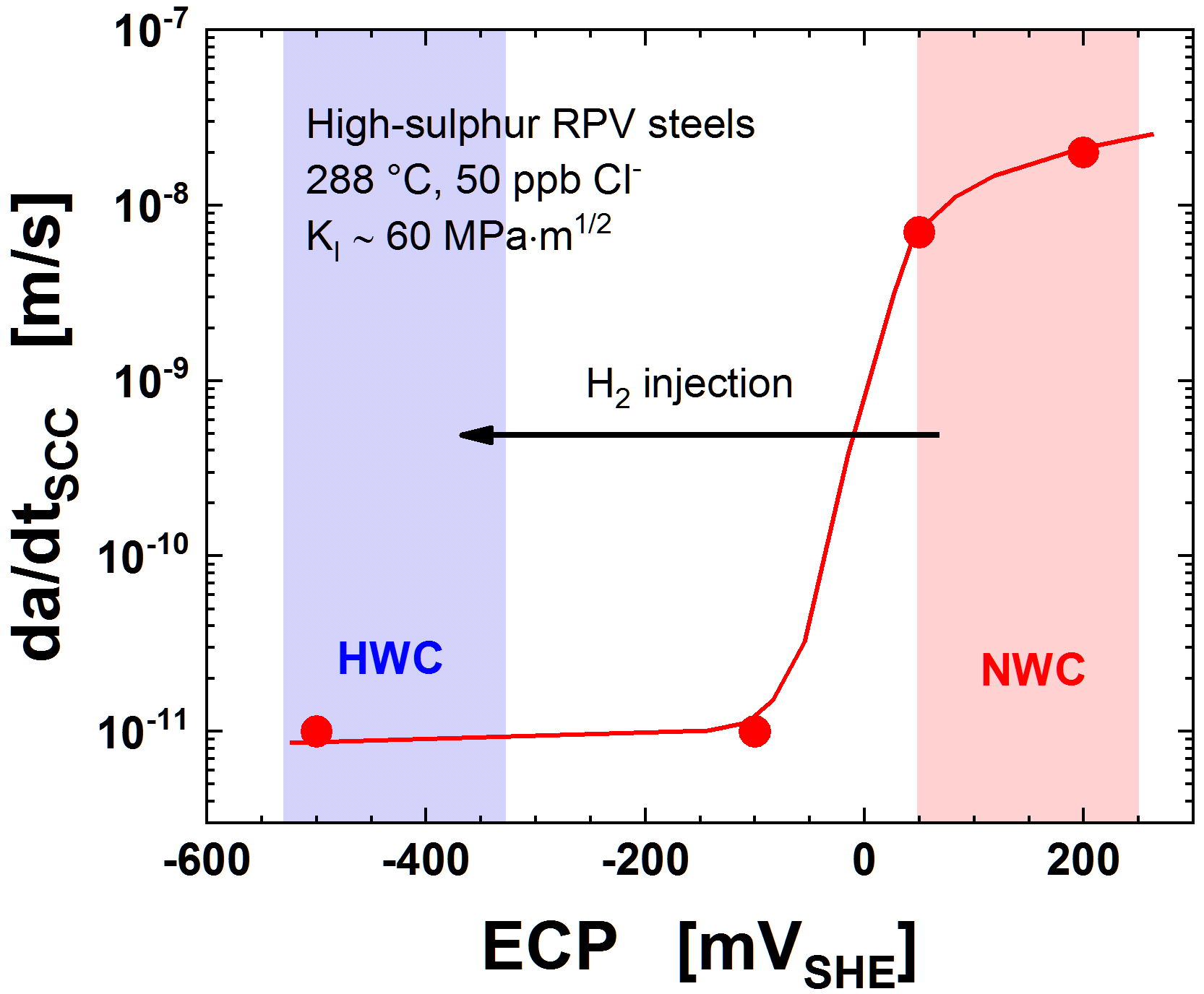
Fig. 3: Mitigation effect of HWC with hydrogen injection into the feedwater on SCC crack growth in RPV steel in case of 50 ppb chloride contamination of the reactor coolant. (© Paul Scherrer Institut)
In BWRs with reducing hydrogen water chemistry (HWC) (as it is applied in the Swiss BWR KKL and KKM) with hydrogen injection into the feedwater, a much higher chloride tolerance was observed (Figure 3), where no SCC occurred in the RPV steel up to high chloride concentrations of 500 ppb.
![Fig. 4: ASME BPV Code Case N-896 SCC disposition curves for RPV steels in BWR/NWC and HWC environment [5]. (© ASME) Fig. 4: ASME BPV Code Case N-896 SCC disposition curves for RPV steels in BWR/NWC and HWC environment [5]. (© ASME)](https://blog.secnrs.ru/wp-content/uploads/2020/10/Article3_pic4.jpg)
Fig. 4: ASME BPV Code Case N-896 SCC disposition curves for RPV steels in BWR/NWC and HWC environment [5]. (© ASME)
![Fig. 5: ASME BPV Code Case N-896 SCC disposition curves for RPV steels during chloride transients in BWR/NWC environment [5]. (© ASME) Fig. 5: ASME BPV Code Case N-896 SCC disposition curves for RPV steels during chloride transients in BWR/NWC environment [5]. (© ASME)](https://blog.secnrs.ru/wp-content/uploads/2020/10/Article3_pic5.jpg)
Fig. 5: ASME BPV Code Case N-896 SCC disposition curves for RPV steels during chloride transients in BWR/NWC environment [5]. (© ASME)
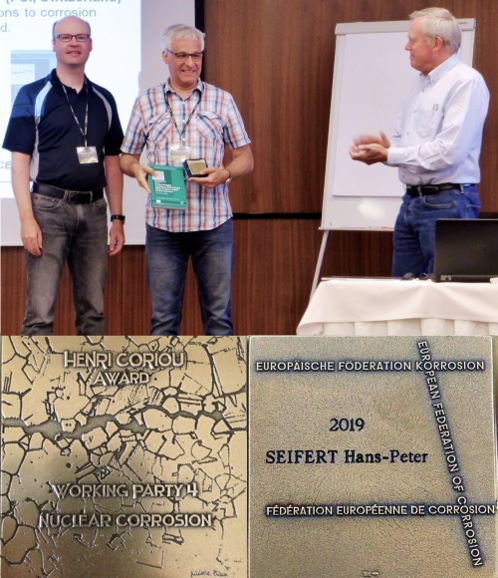
Handover of EFC Coriou Award 2019 to H.P. Seifert by D. Feron (President of the World Corrosion Organization) and S. Ritter (Chairman of the Nuclear Corrosion Working Party of the EFC) during the EFC Nuclear Corrosion Summer School 2019 in Slovenia. (© Paul Scherrer Institut)
Original publications
- H.P. Seifert, S. Ritter, H.J. Leber, S. Roychowdhury, Stress Corrosion Cracking Behavior in the Transition Region of Alloy 182/Low-Alloy Reactor Pressure Vessel Steel Dissimilar Metal Weld Joints in Light Water Reactor Environments, Corrosion 71 (2015) 433-454.
- H.P. Seifert, S. Ritter, The influence of ppb levels of chloride impurities on the stress corrosion crack growth behaviour of low-alloy steels under simulated boiling water reactor conditions, Corrosion Science 108 (2016) 134–147.
- H.P. Seifert, S. Ritter, The influence of ppb levels of chloride impurities on the stain-induced corrosion cracking and corrosion fatigue crack growth behaviour of low-alloy steels under simulated boiling water reactor conditions, Corrosion Science 108 (2016) 148–159.
- H.P. Seifert, S. Ritter, Stress Corrosion Cracking of Low-Alloy Reactor Pressure Vessel Steels under Boiling Water Reactor Conditions, Journal of Nuclear Materials 372 (2008) 114 – 131.
- S. Ranganath, R.G. Carter, R. Pathania, S. Ritter, H.-P. Seifert, Evaluation of Stress Corrosion Crack Growth in Low Alloy Steel Vessel Materials in the BWR Environment, in: Proceedings of the ASME 2018 Pressure Vessels and Piping Conference PVP2018 July 15-20, 2018, Prague, Czech Republic, Paper PVP2018-84257.
Contact: Hans-Peter Seifert, Laboratory for Nuclear Materials (LNM), Paul Scherrer Institut, hans-peter.seifert@psi.ch
Source: ETSON